Champion Business Solutions, LLC
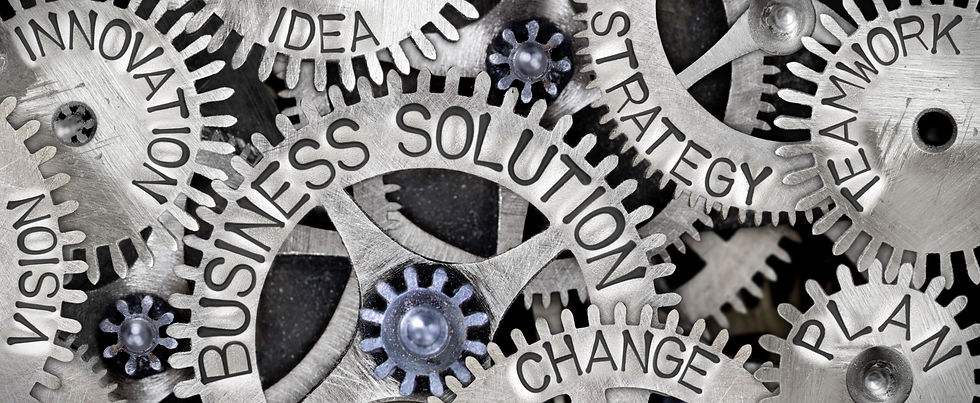
Welcome to Champion Business Solutions, LLC
Warehouse Management
THE 6 WAREHOUSE FUNDAMENTALS

Above: A place for everything, and everything in its place.
The six fundamentals of warehouse management are used in warehouses every day. Understanding these six fundamentals will allow you to streamline your warehouse operations, reduce mistakes, and increase your customer service level. The six fundamentals, or individual, processes are shown in the chevron graphic below. Each is described below.

1. Receiving
Receiving is the first warehouse process and is the most important. If there are mistakes in this process, all of the downward processes will be affected. When receiving material into a warehouse, the clerks should identify the correct item, quantity, and condition. There should also be an incoming inspection procedure. Some things may need a more thorough inspection than others. For example, copy paper may need a cursory look for quantity and damage, while electronics, food, and chemicals need a more thorough and complete incoming inspection process. Inspection codes often determine the level of inspection detail required.​
In some cases, depending on your ERP business software settings, serialized or lotted materials may need to have their respective codes entered at this step. But, again, any mistakes at this step will affect all downward processes. For example, an often overlooked receiving process is customer returns or reverse logistics.
The receiving step is also the best time to apply unique company labels and think about counting this item during cycle counts. Breaking down large bulk into easily measured units will aid in inventory accuracy and the cycle counting process.
​
2. Put Away
Put-Away is the second warehouse process and is essentially moving materials from the receiving dock and inspection areas to the designated warehouse storage or bin location. When materials are put away correctly, there are several benefits:
-
Reduced team member travel in the warehouse
-
Searching for materials is eliminated
-
Material is stored faster and more efficiently
-
Maximized warehouse space utilization
-
Cycle Counting and Physical audits are easier to complete
​
3. Storage
Storage is the warehouse process where materials are stored until they are needed for production or customer orders. When stored properly, the storage process maximizes the available space in your warehouse and will increase labor efficiency.
Every warehouse should have a bird's eye view map that shows the warehouse addressing system for quick put-away and picking. This drawing is to train new employees and locate less-used materials and should be posted throughout the warehouse.
There may be special case situations where some materials should not be stored next to one another (think hazmat), and these items should be set up correctly by bin location in your ERP business software system.
​
4. Picking
The picking process is the warehouse process that retrieves materials in a warehouse to fulfill internal production orders and customer orders. A well-designed warehouse and bin/location addressing system go a long way here. In addition, signage and labeling will aid in locating items to be picked. Finally, the picking process is a good candidate for automation using handheld computers, tablets, and wearable technology.
This area is also often overlooked when reviewing staffing requirements.
5. Packing
Packing is the warehouse process that consolidates picked items in a sales order and prepares them for shipment to the customer. One of the primary tasks of packing is to ensure that damages are minimized from the time items leave the warehouse. Packing can be palletizing or boxing, and it is essential to identify and minimize additional costs for packing materials and labor. For palletizing, shrink-wrap machinery should be used to increase efficiency.
​
6. Shipping
Shipping is the final process at the warehouse. The previous steps, such as receiving, storage, put-away, picking, and packing, are vital to shipping success because they significantly affect whether the order is fulfilled accurately and safely. The shipping process is successful only if the customer receives the right items on time and undamaged.
​
In summary, there is always room for improvement in the six basic warehouse fundamentals. In addition, technology, labor, and the supply chain will keep warehouse managers looking for new ways to increase efficiency and perform their jobs as expected. Therefore, it is a good idea to review the six warehouse fundamentals periodically and see how internal or external changes are affecting your operations.
​
If you would like to review your warehouse processes, please contact us at Champion Business Solutions, LLC, and we will help you review your six fundamentals of warehouse management.
​
​